Org. Synth. 1995, 72, 116
DOI: 10.15227/orgsyn.072.0116
BENZOCYCLOBUTENONE BY FLASH VACUUM PYROLYSIS
[Bicyclo[4.2.0]octa-1,3,5-trien-7-one]
Submitted by Peter Schiess, Ppatibha V. Barve, Franz E. Dussy, and Andreas Pfiffner
1.
Checked by Nobuyoshi Nomura and Hisashi Yamamoto.
1. Procedure
For flash vacuum pyrolysis experiments on a preparative scale the apparatus shown in
Figure 1 is used.
2 It consists of a vertically-mounted assembly of fused silica and
Pyrex tubing 3.2 cm in diameter. The high temperature section
A, 45 cm in length, is made from fused silica. It carries inner 29/32 ground glass joints. The upper evaporation section
B, 25 cm in length, is made of Pyrex. It is fitted with two outer 29/32 ground glass joints
(Note 1). Both tubes are loosely filled with Raschig rings cut from thin-walled, fused silica tubing 1 cm in diameter. The evaporation zone is heated by glass fiber heating tape (180 × 1 cm) controlled by a variac transformer. Heat for the pyrolysis section is provided by an electric tube furnace
(Note 2). The temperature is measured with a thermocouple fixed on the surface of the silica tube in the middle of the hot reaction zone. The substance to be pyrolyzed is added to the evaporator under reduced pressure and at a constant drop rate from a
250-mL, pressure-equalizing dropping funnel C (Note 3). A
250-mL, long-necked, round-bottomed flask D cooled to −78°C serves as a receiver. (
Caution! Flask D (Note 4) must be checked by visual inspection at regular intervals. If condensed product accumulates in the entrance neck, the cooling bath level must be lowered to prevent clogging. Flask D must always be cooled to the neck of the flask. Otherwise material might be transferred from the receiver into trap E, which might then become plugged). Flask
D is connected by a wide glass tube
(Note 4) to a cooling trap
E kept at liquid
nitrogen temperature
(Note 5).
Figure 1
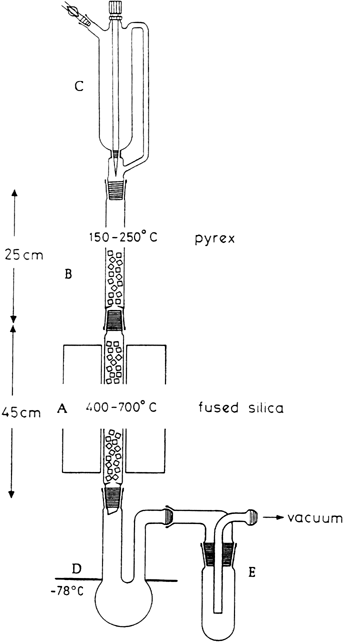
At a pyrolysis oven temperature of 630°C, an evaporator temperature of 200°C, and a pressure of 12 mm, 2-toluic acid chloride (240 g, 1.55 mol) (Note 6) is added in about 2.5 hr at a constant rate of 40–60 drops/min (Note 7). The pressure should be monitored in the addition funnel C during the pyrolysis. A sudden rise in pressure indicates that a restriction is building up between the pyrolysis reactor and the pump. In this case addition of reactant must be stopped. Ten minutes after the addition is complete the apparatus is flushed with nitrogen. The dark brown, oily condensate in the receiver is dissolved in 500 mL of acetone and diluted with 250 mL of cold water (Note 8) and (Note 9). The homogeneous solution is stirred at room temperature for 1 hr. It then is separated into two phases by the addition of 500 mL of 2 N sodium carbonate solution and 250 mL of ether. The aqueous layers are extracted twice with 250-mL portions of ether. The ether extracts are washed with 2 N sodium carbonate solution and with saturated sodium chloride solution. The combined ether layers are dried over sodium sulfate. Removal of the solvent and distillation of the residue yields 65 g of a yellow oil, bp 87–90°C/13 mm, with the following composition: Benzocyclobutenone (97%), benzyl chloride (3%) (Note 10). Fractionation at 12 mm through a 25-cm spinning band column (Note 11) gives 58 g of benzocyclobutenone (>99%) as a colorless oil, bp 84–86°C/12 mm (Note 12) and (Note 13). The product crystallizes at 0°C and then melts at 10–15°C (Note 14).
Most of the acetone is removed from the combined aqueous layers by distillation. Upon acidification with concentrated hydrochloric acid a thick precipitate forms. Filtration and drying leads to 106 g of almost colorless 2-toluic acid, mp 103–107°C. This material is of sufficient purity for conversion into the acid chloride and for subsequent flash vacuum pyrolysis.
2. Notes
1.
Teflon sleeves are used to assure the vacuum tight connection between the ground joints subjected to heat. The checkers used clear-seal joints in all of the glass connections.
2.
Electric tube furnaces of appropriate dimensions are available from various manufacturers. A model RO 4/25 by Heraeus GmbH, Hanau, FRG is suitable. However, a very satisfactory furnace can be built by any well equipped laboratory workshop at little cost and effort. The material required consists of thin walled ceramic tubing, 3.5 cm i.d., nichrome resistance wire, heat resistant insulation, and ordinary hardware material. A technical drawing will be provided by the submitters upon request. The temperature of the furnace can be adjusted by an electronic temperature controller using a thermocouple sensor. A 1.5 kW-Variac transformer and any high temperature
thermometer would do as well for the budget-minded chemist.
3.
A
dropping funnel with a needle valve, NORMAG type 8056, manufactured by NORMAG GmbH, D-6238 Hofheim, FRG, has been used by the submitters. The checkers used a standard pressure-equalizing dropping funnel with a Teflon stopcock.
4.
Receiver
D is a
250-mL, round-bottomed flask with two, 15-cm long necks with a diameter of 3.5 to 5 cm (entrance neck) and 2.5 cm (exit neck) (see
Figure 1). If a receiver
D with a narrower entrance neck than indicated is used the neck can become plugged by condensate. A wide-bore connection is used between receiver
D and the cold
trap E to prevent a pressure drop during pyrolysis, which might be caused by a restriction in the HCl-gas flow.
5.
Caution! Hydrogen chloride (bp −84.9°C) is condensed in trap
E. Exercise care in its disposal.
6.
2-Toluic acid chloride (bp
213–214°C) is prepared from
2-toluic acid (EGA Chemie, Steinheim, FRG) by treatment with
thionyl chloride (SOCl
2). The checkers purchased the acid chloride from Tokyo Chemical Co.
7.
The pyrolysis temperature and the rate of addition are chosen such that about 50% of the acid chloride is recovered as
2-toluic acid after hydrolysis. Under these conditions only a small amount of
benzyl chloride and polymeric material is formed in addition to
benzocyclobutenone. The percentage of reactant conversion depends not only on the pyrolysis temperature, but also on the pressure in the reactor and on the rate of reactant addition. It is advisable, therefore, to optimize the pyrolysis temperature in trial runs keeping the other variables constant.
In the runs carried out by the checkers, conversion of reactant was slightly lower than 50% as shown by the recovery of 2-toluic acid in 63–74% yield. In these runs benzocyclobutenone was obtained in 17–20% yield only. However, the yield calculated with respect to reactant consumed and not recovered as 2-toluic acid amounted to 56–64% and thus did not differ significantly from the value given in the procedure.
8.
If separation into two phases occurs,
acetone is added until a homogeneous solution results.
9.
Hydrolysis of unreacted acid chloride is carried out without neutralization of the acid generated. In the presence of a base such as
sodium carbonate or
sodium bicarbonate the anhydride of
2-toluic acid would be formed, in addition to the sodium salt of the free acid. This anhydride is much less reactive toward hydrolysis than the acid chloride.
10.
VPC analyses were performed using a
PEG column of 25 m × 0.25 mm.
11.
A
25-cm spinning band column of 12 theoretical plates, manufactured by NORMAG GmbH, D-6238 Hofheim, FRG, has been used by the submitters. The checkers found a
30-cm Vigreux distillation column just as suitable for the separation.
12.
A forerun, 4.9 g of a yellow oil, bp 52–85°C/12 mm, consisting of a mixture of
benzyl chloride and
benzocyclobutenone, is discarded.
13.
This corresponds to a yield of
benzocyclobutenone, >99% homogeneous by VPC, of 32% with respect to the
2-toluic acid chloride subjected to pyrolysis, and of 63% with respect to the
2-toluic acid chloride consumed in the reaction.
14.
The spectral properties are as follows:
1H NMR (CDCl
3, 300 MHz) δ: 4.00 (s, 2 H), 7.34–7.45 (m, 2 H), 7.50–7.57 (m, 2 H); IR (liquid film) cm
−1: 3060, 2920, 1780, 1760, 1585, 955, and 755.
Handling and Disposal of Hazardous Chemicals
The procedures in this article are intended for use only by persons with prior training in experimental organic chemistry. All hazardous materials should be handled using the standard procedures for work with chemicals described in references such as "Prudent Practices in the Laboratory" (The National Academies Press, Washington, D.C., 2011 www.nap.edu). All chemical waste should be disposed of in accordance with local regulations. For general guidelines for the management of chemical waste, see Chapter 8 of Prudent Practices.
These procedures must be conducted at one's own risk. Organic Syntheses, Inc., its Editors, and its Board of Directors do not warrant or guarantee the safety of individuals using these procedures and hereby disclaim any liability for any injuries or damages claimed to have resulted from or related in any way to the procedures herein.
3. Discussion
Benzocyclobutenone was first prepared from
1-bromobenzocyclobutene by hydrolysis followed by
chromium trioxide oxidation.
3 4,5 More recent procedures involve hydrolysis of
1,1-dichloro- or 1,1-dimethoxybenzocyclobutene which in turn have been obtained through cycloaddition of the appropriate 1,1-disubstituted ethylenes to
benzyne generated either from
anthranilic acid through diazotization
6,7 or from
bromobenzene through
sodium amide treatment.
8,9 Benzocyclobutenone has also been obtained through flash vacuum pyrolysis from homophthalic anhydride,
10 from
indane-1,2-dione,
11 and from
2-trimethylsilylmethylbenzoyl chloride.
12
The present pyrolytic method is based on a communication by the authors
13 with some modifications of the pyrolysis apparatus for preparative scale.
14 This method is applicable to the preparation of benzocyclobutenones carrying various substituents on the aromatic ring (see Table). Its merit lies in its simplicity for generating the strained bicyclic ring system from inexpensive precursors. Benzocyclobutenones in general are thermolabile, losing
carbon monoxide at higher temperature.
11 It therefore is advisable to keep thermolytic conversion below 100%. Unconverted starting material can be recovered after hydrolysis of the crude reaction mixture as carboxylic acid and reused for the conversion to acid
chloride without further purification. Gas phase pyrolysis has been available as a preparative method in organic chemistry for a long time.
15 Various procedures using this method have been described in previous volumes of
Organic Syntheses.
16 17 18 19 20 21 22 23 Several reviews describing applications of the pyrolytic method in preparative organic chemistry have appeared in recent years.
24 25
TABLE
BENZOCYCLOBUTENONES PREPARED THROUGH FLASH VACCUM PYROLYSIS OF 2-METHYLBENZOIC ACID CHLORIDES14,16,17,18,19,20,21,22,23
|
|
2
|
3
|
4
|
5
|
Reaction Conditions (°C/mm)
|
Acid Recovered, %
|
Yielda %
|
mp (°C)
|
|
H
|
H
|
H
|
H
|
630/13
|
50
|
65
|
10–15
|
H
|
CH3
|
H
|
CH3
|
560/13
|
5
|
77
|
47–48
|
CH3
|
CH3
|
CH3
|
CH3
|
550/13
|
-
|
83
|
156–157
|
H
|
O-CH2-O
|
H
|
570/13
|
12
|
81
|
122–124
|
H
|
OCH3
|
H
|
H
|
570/13
|
41
|
67
|
49–50
|
H
|
H
|
H
|
OCH3
|
590/0.1
|
51
|
63
|
32–33
|
OCH3
|
H
|
H
|
OCH3
|
590/0.1
|
20
|
63
|
106–107
|
H
|
OCH3
|
OCH3
|
H
|
530/13
|
57
|
37
|
142–143
|
H
|
H
|
CH=CH-CH=CH
|
550/13
|
11
|
82
|
96–97
|
|
aYield of purified ketone with respect to acid chloride consumed and not recovered as acid after hydrolysis.
|
Appendix
Chemical Abstracts Nomenclature (Collective Index Number);
(Registry Number)
1,1-dichloro- or 1,1-dimethoxybenzocyclobutene
hydrogen chloride,
hydrochloric acid (7647-01-0)
benzyne (71-43-2)
ether (60-29-7)
carbon monoxide (630-08-0)
thionyl chloride (7719-09-7)
sodium bicarbonate (144-55-8)
sodium chloride (7647-14-5)
sodium carbonate (497-19-8)
sodium sulfate (7757-82-6)
nitrogen (7727-37-9)
acetone (67-64-1)
benzyl chloride (100-44-7)
bromobenzene (108-86-1)
Anthranilic Acid (118-92-3)
chloride
chromium trioxide (1333-82-0)
sodium amide (7782-92-5)
1-bromobenzocyclobutene
Benzocyclobutenone
Bicyclo[4.2.0]octa-1,3,5-trien-7-one (3469-06-5)
2-toluic acid chloride (933-88-0)
2-toluic acid (118-90-1)
indane-1,2-dione
2-trimethylsilylmethylbenzoyl chloride
Copyright © 1921-, Organic Syntheses, Inc. All Rights Reserved