Org. Synth. 1972, 52, 90
DOI: 10.15227/orgsyn.052.0090
DIETHYLALUMINUM CYANIDE
[Aluminum, cyanodiethyl-]
Submitted by W. Nagata
1 and M. Yoshioka.
Checked by S. C. Welch, P. Bey, and Robert E. Ireland.
1. Procedure
Caution! Dialkylzinc compounds, especially in undiluted form, are pyrophoric and must not be allowed to come into contact with air or moisture. These compounds should only be handled by individuals trained in their proper and safe use. [Note added January 2011]
Caution! This preparation should be conducted in a well-ventilated hood, and neat triethylaluminum must be handled with great care.
Benzene has been identified as a carcinogen. OSHA has issued emergency standards on its use. All procedures involving benzene should be carried out in a well-ventilated hood, and glove protection is required.
A
tared, 500-ml., round-bottomed flask is fitted with a vacuum take-off, and the entire assembly is connected through an
adaptor containing a stopcock to an inverted cylinder of triethylaluminum, as shown in
Figure 1. The assembly is connected to a
nitrogen source
(Note 1) through the vacuum take-off, and with the cylinder valve closed but the stopcock open, the system is alternately evacuated and filled with
nitrogen four times. With the system filled with
nitrogen the cylinder valve is opened and approximately
55 ml. (46 g; 0.40 mole) of triethylaluminum (Note 2) is allowed to flow into the reaction flask. The cylinder valve is then closed; the system is evacuated and filled three times with
nitrogen, and the adaptor stopcock is then closed
(Note 3). The reaction flask is then quickly removed, stoppered, and weighed to determine the exact amount of
triethylaluminum collected. A
magnetic stirring bar is added and the flask is fitted with a vacuum take-off and
250-ml., pressure-equalizing dropping funnel. The system is again placed under a
nitrogen atmosphere, and the
triethylaluminum is dissolved in
150 ml. of anhydrous benzene, added through the dropping funnel. The dropping funnel is charged with a solution of
11.9 g. (0.441 mole) of hydrogen cyanide (Note 4) in
100 ml. of anhydrous benzene, which is added dropwise to the solution of
triethylaluminum, with stirring and cooling. Preferably, the addition is carried out at a constant rate such that the
hydrogen cyanide solution is added in about 2 hours. The evolution of
ethane becomes slow suddenly after one molar equivalent of
hydrogen cyanide is added
(Note 5). After the addition is complete, the reaction mixture is allowed to stir overnight
(Note 6).
Figure 1. Apparatus for collection of triethylaluminum.
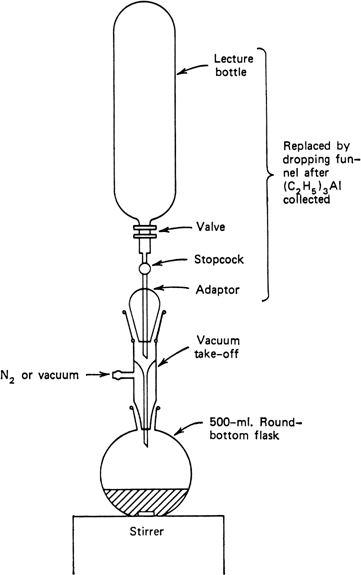
After this period, the dropping funnel and the vacuum take-off are replaced by the short-path distillation assembly shown in
Figure 2. The system is protected with a Drierite tube, and the
benzene is distilled under reduced pressure (
water aspirator). After the
benzene is removed, the
benzene-containing receiver is replaced with a clean, dry flask, and the system is connected to an
efficient vacuum pump. The pressure in the system is reduced to 0.02 mm., and the flask is immersed deeply in an
oil bath (
Figure 2) heated to about 200°. After about 1 ml. of forerun is collected,
diethylaluminum cyanide distils at
162° (0.02 mm.) (Note 7) and is collected in a tared,
200-ml. receiver by heating the side arm and the adaptor with a stream of hot air or an IR lamp
(Note 8). After all the distillate is collected in the receiver
(Note 9), dry
nitrogen is admitted to the evacuated apparatus, and the receiver is stoppered, giving
26.7–35.6 g. (
60–80%) of
diethylaluminum cyanide, usually as a pale, yellow syrup
(Note 10) and
(Note 11).
>Figure 2. Short-path distillation apparatus.
The stopper of the flask is quickly replaced with the nitrogen adaptor, and after placing the system under a nitrogen atmosphere, the diethylaluminum cyanide is treated with 130 ml. of dry benzene. The resulting mixture is allowed to stand with occasional swirling under nitrogen until the syrup goes into solution (Note 12). Sufficient dry benzene is then added to make the total volume of the solution 200 ml. After thorough mixing with a magnetic stirring bar, the resulting diethylaluminum cyanide solution (13.4–17.8%; 1.2–1.6 M) may be divided and stored in sealed ampoules (Note 13).
2. Notes
2.
The exact volume of the
triethylaluminum added at this point is not critical, since the exact weight is determined later. The use of a
25% solution of triethylaluminum in benzene, available from the Stauffer Chemical Company, 299 Park Avenue, New York, eliminates the tedious preparation of the
triethylaluminum solution described in this procedure.
3.
These precautions will ensure the removal of any adhering
triethylaluminum that will flame when the apparatus is disassembled.
4.
A
10% molar excess of hydrogen cyanide was employed, and the quantity added at this point was determined by the amount of
triethylaluminum collected.
Hydrogen cyanide can be prepared as described in
Tetrahedron Lett., 461 (1962).
5.
The change in the rate of gas evolution is sometimes not clear, especially when the temperature of the hood is high. When the change is recognized distinctly, the addition of
hydrogen cyanide solution may be stopped.
6.
The reaction mixture containing about
13% (1.2 M) of diethylaluminum cyanide and a small amount of
ethylaluminum dicyanide may be used for most hydrocyanation processes without further purification. Care must be taken to have no unchanged
triethylaluminum, since the submitters have observed that hydrocyanation of Δ
8-11-keto steroids with
diethylaluminum cyanide is greatly retarded by the presence of a small amount of unchanged
triethylaluminum.
2,3
7.
The checkers collected
diethylaluminum cyanide at
170–180° (0.35 mm.) and
167–175° (0.25 mm.).
8.
Heating of the glassware above 150° with a hot air stream or IR lamp is needed to make the viscous product run into the receiver.
9.
The pot residue contains
ethylaluminum dicyanide as a nonvolatile mass, most of which may be removed with a
spatula and decomposed with
isopropyl alcohol and then water. The flask is then washed with running water and
20% hydrochloric acid to remove the mass completely.
10.
The submitters have obtained an almost colorless syrup by reaction of purified
triethylaluminum with
hydrogen cyanide, followed by repeated distillation.
11.
The yield depends on the efficiency of the collection of the viscous distillate in the receiver.
12.
It takes considerable time (5–10 hours) to dissolve
diethylaluminum cyanide. Magnetic stirring is not effective unless most of the material goes into solution.
13.
Diethylaluminum cyanide dissolved in
benzene,
toluene,
hexane, or
isopropyl ether and stored in ampoules is stable for a long period. The cyanide is not stable in
tetrahydrofuran. The anhydrous
benzene used in the reaction may be replaced by
diethyl or diisopropyl ether. A
1–2 M solution of diethylaluminum cyanide in benzene is commercially available from Alfa Products, Ventron Corporation, Danvers, Massachusetts.
3. Discussion
Formation of
diethylaluminum cyanide from
triethylaluminum and
hydrogen cyanide was noted initially by the submitters
4 and later by Stearns,
5 but isolation and characterization of the product were first performed by the submitters.
3 An impractical process comprised of heating
diethylaluminum chloride and
sodium cyanide in
benzene for 21 days has been reported.
6
Diethylaluminum cyanide is a useful, potent reagent for hydrocyanation of various compounds. Features of this reagent as compared with the
triethylaluminum–
hydrogen cyanide reagent may be obtained from the literature.
2,3,7
This preparation is referenced from:
Appendix
Chemical Abstracts Nomenclature (Collective Index Number);
(Registry Number)
diethyl or diisopropyl ether
hydrochloric acid (7647-01-0)
Benzene (71-43-2)
sodium cyanide (143-33-9)
hydrogen cyanide (74-90-8)
nitrogen (7727-37-9)
toluene (108-88-3)
isopropyl alcohol (67-63-0)
ethane (74-84-0)
Tetrahydrofuran (109-99-9)
isopropyl ether (108-20-3)
hexane (110-54-3)
triethylaluminum (97-93-8)
Diethylaluminum cyanide (5804-85-3)
Aluminum, cyanodiethyl-
ethylaluminum dicyanide
diethylaluminum chloride
Copyright © 1921-, Organic Syntheses, Inc. All Rights Reserved