Org. Synth. 2005, 81, 195
DOI: 10.15227/orgsyn.081.0195
OXIDATION OF PRIMARY ALCOHOLS TO CARBOXYLIC ACIDS WITH SODIUM CHLORITE CATALYZED BY TEMPO AND BLEACH: 4-METHOXYPHENYLACETIC ACID
[(Benzeneacetic acid, 4-methoxy-)]
Submitted by Matthew M. Zhao
1, Jing Li
1, Eiichi Mano
2, Zhiguo J. Song
1, and David M. Tschaen
1.
Checked by Arun Ghosh, Jamie Sieser, Weiling Cai, and Sarah E. Kelly.
1. Procedure
A 1-L, three-necked, round-bottomed flask equipped with a mechanical stirrer and two 100-mL addition funnels is charged with 4-methoxyphenethyl alcohol (1f) (6.09 g, 40 mmol), TEMPO (2,2,6,6-tetramethyl-1-piperidinyloxy free radical) (0.436 g, 2.8 mmol), 200 mL of acetonitrile, and 150 mL of 0.67M sodium phosphate buffer (pH 6.7) (Notes 1, 2). A solution of sodium chlorite is prepared by dissolving 80% NaClO2 (9.14 g, 80.0 mmol) in 40 mL of water and a solution of dilute sodium hypochlorite (NaOCl) is prepared by diluting household bleach (5.25 NaOCl, 1.06 mL, ca. 2.0 mol%) with 19 mL of water. The reaction mixture is heated to 35°C with stirring and approximately 20% of the NaClO2 solution is added via one addition funnel followed by 20% of the dilute bleach solution via the other funnel. The remaining portions of both reagents are then added simultaneously over 2 hr (Note 3). The resulting mixture is stirred at 35°C until the reaction is complete (Note 4) (usually 6-10 hr). After cooling the reaction mixture to 25°C, 300 mL of water is added and the pH is adjusted to 8.0 by addition of ca. 48 mL of 2.0N NaOH. The reaction mixture is then poured into ice-cold sodium sulfite solution (12.2 g in 200 mL of water) maintained below 20°C with an ice-water bath (Note 5). After stirring for 0.5 hr at rt, 200 mL of methyl t-butyl ether (MTBE) is added and the resulting mixture is stirred for 15 min. The organic layer is separated and discarded. More MTBE (100 mL) is added and the rapidly stirred mixture is acidified with 2.0N HCl to pH 3-4. The organic layer is separated and the aqueous layer is extracted with two 100-mL portions of MTBE. The combined organic phases are washed with two 100-mL portions of water, 100 mL of brine, and then concentrated to give 6.16-6.22 g (93-94%) of 4-methoxyphenylacetic acid (2f) as a colorless solid (Note 6).
2. Notes
1.
All reactants and reagents were obtained from Sigma-Aldrich and used without purification.
2.
The
sodium phosphate buffer consisted of a
1:1 mixture of 0.67M NaH2PO4 and 0.67M Na2HPO4 (pH = 6.5 at 22°C). For substrates not prone to chlorination, lower pH (3-4) can be employed to speed up the reaction.
3.
Caution: it is not advisable to mix sodium chlorite solution and bleach prior to the addition since the mixture appears to be unstable. On a small scale, it is acceptable to mix the substrate, sodium chlorite, TEMPO, acetonitrile, and buffer first and then add bleach in one portion.
4.
The progress of the reaction is monitored by HPLC: YMC ODS-AM column, 4.6 × 250mm, flow rate 1.00mL/min, 30°C, linear gradient 20-80% MeCN/15min, 0.1% H
3PO
4; retention time
1f: 9.09 min,
2f: 9.25 min.
5.
The pH of the aqueous layer should be 8.5 - 9.0.
6.
The product exhibits the following properties:
mp 86-88.5°C (lit.
9 86°C);
1H NMR
pdf (400 MHz, CDCl
3) δ: 3.59 (s, 2H), 3.79 (s, 3H), 6.88 (d, J = 8.5, 2H), 7.19 (d, J = 8.5, 2H);
13C NMR (100 MHz, CDCl
3) δ: 178.4, 159.1, 130.7, 125.5, 114.3, 55.5, 40.4; HPLC purity >99 area %.
Handling and Disposal of Hazardous Chemicals
The procedures in this article are intended for use only by persons with prior training in experimental organic chemistry. All hazardous materials should be handled using the standard procedures for work with chemicals described in references such as "Prudent Practices in the Laboratory" (The National Academies Press, Washington, D.C., 2011 www.nap.edu). All chemical waste should be disposed of in accordance with local regulations. For general guidelines for the management of chemical waste, see Chapter 8 of Prudent Practices.
These procedures must be conducted at one's own risk. Organic Syntheses, Inc., its Editors, and its Board of Directors do not warrant or guarantee the safety of individuals using these procedures and hereby disclaim any liability for any injuries or damages claimed to have resulted from or related in any way to the procedures herein.
3. Discussion
The procedure described here provides an efficient and environmentally benign method for oxidizing primary alcohols to carboxylic acids using stoichiometric
NaClO2, catalytic TEMPO, and NaOCl. Compared with the previously reported
TEMPO/NaOCl/CH2Cl2 protocol,
5c this new procedure gives significantly improved yields and purity of the desired product by reducing the chlorination of the aromatic groups. No racemization or epimerization is observed for substrates with labile chiral centers. Additionally, no chlorinated solvent is required. Similar to
TEMPO/NaOCl, this procedure is not applicable to alkenic alcohols and substrates with exceedingly electron-rich aromatic groups.
The development of this procedure stems from our recent work involving the oxidation of primary alcohol
1 to the carboxylic acid
2.
3
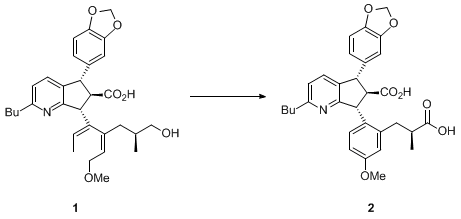
The submitters found that the
RuCl3/H5IO6 protocol
4 gave low yields (
<50%) due to the destruction of the electron-rich aromatic rings.
TEMPO catalyzed oxidation
5 with
NaOCl also gave unsatisfactory results because of the chlorination of the aromatic groups. Other oxidants, such as H
2O
2, MeCO
3H, t-BuO
2H, etc., were examined without much success. In the submitters' recent report
7 on a
CrO3 (1 mol%) catalyzed oxidation, although it is much improved over the Jones oxidation in terms of environmental impact, the heavy metal issue is not completely eliminated. Investigation of the
TEMPO/NaOCl protocol using
sodium chlorite (NaClO2)8 as the oxidant resulted in the development of this new procedure
3b. The reaction appeared to be very slow (~2%/hr) initially. Subsequently, it was found that
NaOCl dramatically accelerated the reaction. The conversion reached
>50% in 1 hr and went to completion in 2-4 hr.
The remarkable acceleration can be explained by the proposed catalytic cycle shown in Scheme 1.
TEMPO radical is first oxidized by
NaOCl to the N-oxoammonium ion
5 A, which rapidly oxidizes the
primary alcohol (1) to the
aldehyde (3) and gives a molecule of the
hydroxylamine D.
5 The
aldehyde (3) is then oxidized by
NaClO2 to the
carboxylic acid (2)6 and regenerates a molecule of
NaOCl. The
hydroxylamine D can either be directly oxidized to
A or undergo a syn proportionation with a molecule of
A to give two molecules of
TEMPO radical which can be oxidized back to
A5a,b Although the exact mechanism of
TEMPO-catalyzed oxidation of alcohols is still unclear, previous work
5 has shown that
N-oxoammonium ion A and
hydroxylamine D are involved. It is also known that
NaClO2 can readily oxidize aldehydes to the carboxylic acids in the absence of
TEMPO.
6 The long induction period of the reaction without a catalytic amount of bleach is likely due to the relatively slow oxidation of
TEMPO radical or the
hydroxylamine D by
NaClO2. Once the reaction is initiated, it becomes self-sustaining as NaOCl is continuously regenerated. The chlorination problem is greatly reduced because the concentration of NaOCl remained low throughout the reaction. Risks for epimerization of the neighboring chiral center are also reduced since the labile aldehyde intermediate is rapidly oxidized to the carboxylic acid by
sodium chlorite.
Scheme 1. Catalytic Cycle for the TEMPO/NaOCl Catalyzed Oxidation
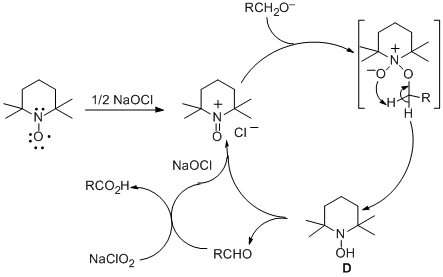
This method is mild and efficient and has been demonstrated on a variety of primary alcohols (Table 1). For comparison purposes, substrates with electron-rich aromatic rings were also subjected to the TEMPO/NaOCl oxidation
5c (entries 3, 5-7, 10). In all of these cases, much improved yields were obtained with this new procedure. The most striking example is
1g. The yield of the desired product
2g was only
42% using stoichiometric NaOCl in contrast to the quantitative yield obtained using our procedure (entry 7). One of the major side products in the oxidation with stoichiometric NaOCl was isolated and identified as the chlorinated compound
4 (Figure 1) based on NMR studies (NOE). Similarly,
3-phenylpropargyl alcohol (
1h) was oxidized to the acid
2h in
90% yield using our procedure vs. < 5% with NaOCl. It appeared that carbon-carbon triple bonds can be tolerated, but substrates with ordinary carbon-carbon double bonds such as
cinnamyl alcohol failed to react. This was likely due to quenching of the catalytic NaOCl, which shut down the catalytic cycle. Substrates with very electron-rich aromatic groups such as
1n-
1o (Figure 1) also failed for similar reasons. Surprisingly, oxidation of
4-methoxybenzyl alcohol (
1p) was very sluggish. Substrate
1i, which contained a cyclopropyl group, posed no problem (entry 9). Chiral alcohols, including protected amino alcohol
1l, were oxidized to the corresponding carboxylic acids without racemization (or epimerization) of the labile chiral centers (entries 10-12).
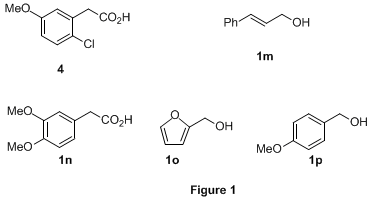
Table 1. TEMPO Catalyzed Oxidation of Primary Alcohols
aAll entries except 3, 9 and 10 were checked. The reactions took 6-10 h for completion in all cases. Additional charges of both NaOCl2 and NaOCL, however, showed faster rate. Entry 11 was particularly sluggish towards oxidation. Yields and purities of products were generally comparable to those reported in the Table. For substrates not prone to chlorination, lower pH (3-4) can be employed to speed up the reaction.
Appendix
Chemical Abstracts Nomenclature (Collective Index Number);
(Registry Number)
4-Methoxyphenethyl alcohol:
Benzeneethanol, 4-methoxy-; (702-23-8).
4-Methoxyphenylacetic acid:
Benzeneacetic acid, 4-methoxy-; (104-01-8).
2,2,6,6-Tetramethyl-1-piperidinyloxy (TEMPO):
1-Piperidinyoxy, 2,2,6,6- tetramethyl-; (2564-83-2).
Sodium chlorite:
Chlorous acid, sodium salt; (7758-19-2).
Sodium hypochlorite:
Hypochlorous acid, sodium salt; (7681-52-9).
Methyl tert-butyl ether;
Propane, 2-methoxy-2-methyl-; (1634-04-4).
Copyright © 1921-, Organic Syntheses, Inc. All Rights Reserved