Org. Synth. 2012, 89, 105-114
DOI: 10.15227/orgsyn.089.0105
2-Iodoxy-5-Methylbenzenesulfonic Acid-Catalyzed Selective Oxidation of 4-Bromobenzyl Alcohol to 4-Bromobenzaldehyde or 4-Bromobenzoic Acid with Oxone
Submitted by Muhammet Uyanik and Kazuaki Ishihara.*
1.
Checked by Margaret Faul and Richard Crockett.
Discussion
Caution! Although no problems were encountered with the explosion of Oxone or other chemicals in the use of this oxidation procedure, prudence dictates that all operations should be conducted in a hood.
A. 4-Bromobenzaldehyde. A 500-mL, three-necked, round-bottomed flask equipped with an overhead mechanical stirrer, a reflux condenser fitted with a nitrogen inlet adapter, and a glass stopper (Note 1) is charged with Oxone (12.8 g, 20.9 mmol, 0.65 equiv) (Notes (Note 2) and (Note 3)) and acetonitrile (70 mL) (Note 4). The mixture is stirred vigorously (1000 rpm) (Notes (Note 5) and (Note 6)) at room temperature for 2 h. To the resulting white suspension are added potassium 2-iodo-5-methylbenzenesulfonate (0.11 g, 0.32 mmol, 1 mol%) (Note 7) and 4-bromobenzyl alcohol (6.00 g, 32.1 mmol) (Note 8), and the wall of the flask is washed with acetonitrile (10 mL) (Note 9). The resulting mixture is heated to 70 °C in an oil bath and stirred vigorously (1000 rpm) (Note 5). After 5 h (Note 10), the resulting white suspension is cooled to room temperature and filtered through a plug of tightly packed Celite (Note 11) on a sintered glass funnel, which is successively washed with diethyl ether (100 mL). To the filtrate is added water (150 mL), and the aqueous layer is separated and extracted with EtOAc (2 x 100 mL). The combined organic layers are washed with saturated aqueous NaHCO3 (100 mL), saturated aqueous Na2SO3 (100 mL), water (100 mL) and saturated brine (100 mL). The resulting organic layers are dried over anhydrous Na2SO4, filtered and concentrated by rotary evaporation (30 °C, 20 mmHg) to give a white solid (5.78-6.25 g) (Note 12). The solid is transferred to a 250-mL, round-bottomed flask. Methanol (40 mL) and deionized water (20 mL) are added, and the mixture is heated to 70 °C until all solids are completely dissolved (Note 13). To the resulting solution is added additional deionized water (30 mL) all at once. The resulting suspension is cooled to 25 °C over 1.5 h and allowed to stir at room temperature (> 3 h) to give a white precipitate. The solids are collected by suction filtration on a Büchner funnel. The reaction flask is rinsed with 50 mL water. This rinse is used to wash the wet cake and collected with the filtrate. The cake is allowed to dry on the funnel for 1 h under vacuum suction with a nitrogen bag fitted over the funnel. The cake is then transferred to a 150-mL, round-bottomed flask and further dried for 12 h (25 °C, 1 mmHg) to provide 4-bromobenzaldehyde (4.45-4.73 g, 24.0-25.6 mmol, 76-80% yield) as a white powder (Notes (Note 14) and (Note 15)). Solids that formed in the first filtrate are collected by suction filtration on a Büchner funnel, washed with water (30 mL), and then transferred to a 150-mL, round-bottomed flask and dried for 12 h (25 °C, 1 mmHg) to provide further 4-bromobenzaldehyde (0.25-0.41 g, 0.97-1.35 mmol, 3-4% yield) as a white powder. The combined yield of 4-bromobenzaldehyde (4.63-4.98 g, 25.0-26.9 mmol) is 79-85% (Notes (Note 14) and (Note 15)).
B. 4-Bromobenzoic acid. A 500-mL, three-necked, round-bottomed flask equipped with an overhead mechanical stirrer, a reflux condenser fitted with a nitrogen inlet adapter, and a glass stopper (Note 1) is charged with Oxone (25.7 g, 41.7 mmol, 1.3 equiv) (Notes (Note 2) and (Note 3)) and acetonitrile (70 mL) (Note 4). The mixture is stirred vigorously (1000 rpm) (Notes (Note 5) and (Note 6)) at room temperature for 2 h. To the resulting white suspension are added potassium 2-iodo-5-methylbenzenesulfonate (0.11 g, 0.32 mmol, 1 mol%) (Note 7) and 4-bromobenzyl alcohol (6.00 g, 32.1 mmol) (Note 8), and the wall of the flask is washed with acetonitrile (10 mL) (Note 9). The resulting mixture is heated to 70 °C in an oil bath and stirred vigorously (1000 rpm) (Notes (Note 5)). After 2.6 h (Note 16), the starting materials are consumed completely. To the mixture is added deionized water (100 mL), and the resulting mixture is stirred vigorously (1000 rpm) at 70 °C. After 6.5 h, TLC showed no aldehyde and HPLC analysis showed < 5 area % of aldehyde. The resulting pale yellow mixture is cooled to room temperature. EtOAc (200 mL) and water (100 mL) are added, and the mixture is transferred to a 1-L separatory funnel. The aqueous layer is separated and extracted with EtOAc (3 x 100 mL). The combined organic layers are washed with saturated aqueous NaHSO3 (100 mL), water (100 mL) and saturated brine (100 mL). The resulting organic layers are dried over anhydrous Na2SO4, filtered and concentrated by rotary evaporation (30 °C, 20 mmHg) to give a pale yellow solid (6.14-6.37 g). The solid is transferred to a 250-mL, round-bottomed flask. Methanol (120 mL) and deionized water (5 mL) are added, and the mixture is heated to reflux (66 °C) to afford a turbid solution. The solution is cooled to room temperature over 1.5 h and aged for 15 min. To the resulting suspension is added additional deionized water (95 mL) over 2 h and the mixture is stirred at room temperature overnight to give pale yellow crystals. The crystals are collected by suction filtration on a Büchner funnel. The reaction flask is rinsed with 50 mL water. This rinse used to wash the wet cake and collected with the filtrate. The cake is allowed to dry on the funnel for 1 h under vacuum suction with a nitrogen bag fitted over the funnel. The cake is then transferred to a 150-mL, round-bottomed flask and further dried for 12 h (25 °C, 1 mmHg) to provide 4-bromobenzoic acid (5.28-5.5 g, 26.3-27.6 mmol, 83-87% yield) as pale yellow powder (Notes (Note 13) and (Note 16)). Solids that formed in the first filtrate are collected by suction filtration on a Büchner funnel, washed with water (50 mL), and then transferred to a 100-mL, round-bottomed flask and dried for 12 h (25 °C, 1 mmHg) to provide further 4-bromobenzoic acid (0.18-0.19 g, 0.89-0.94 mmol, 2-3% yield) as pale yellow powder. The combined yield of 4-bromobenzoic acid (5.47-5.73 g, 27.2-28.5 mmol) is 86-90% (Note (Note 14) and (Note 17)).
2. Notes
1.
A glass stir bearing with a ground glass stir shaft (10 mm diameter) and stir lube was used. To the stir shaft was affixed a semi circular, Teflon stir paddle (19 x 60 mm).
2.
Oxone (2KHSO
5·KHSO
4·K
2SO
4) was purchased from Aldrich Chemical Company, Inc., and used as received.
3.
Although no problems were encountered with the explosion of Oxone or other chemicals in the use of this oxidation procedure, prudence dictates that all operations should be conducted in a hood.
4.
Analytical reagent-grade acetonitrile was purchased from the Aldrich Chemical Company and used as received.
5.
Oxone was almost insoluble in acetonitrile. Although Oxone adhered to the wall of the flask during the reaction, vigorous stirring (=800 rpm) is preferred for efficient grinding of Oxone and efficient alcohol oxidation.
6.
Due to very turbulent mechanical stirring and vibrations, and to prevent leakage of solvent and compounds, it is necessary prepare all flask joints as follows: apply grease and wrap in Teflon tape followed by parafilm. The stir bearing was secured to the flask with copper wire to prevent separation from flask.
7.
Potassium 2-iodo-5-methylbenzenesulfonate (
99.6%) was obtained from the Aldrich Chemical Company and used as received.
8.
4-Bromobenzyl alcohol (99%) was purchased from the Aldrich Chemical Company and used as received.
9.
The starting material and
pre-catalyst adhered to the wall of the flask. Thus, the wall was washed with additional acetonitrile.
10.
The progress of the reaction is followed by TLC analysis on silica gel with 20% EtOAc-hexane as an eluent and visualization with a UV lamp at 254 nm and molybdatophosphoric acid. The alcohol starting material has R
f = 0.18 and the aldehyde product has R
f = 0.54.
11.
Celite (
~6 g) was used pre-wetted with acetonitrile.
12.
Evaluation of aldehyde volatility: The aldehyde (
961 mg) was placed under house vacuum (20~40 mmHg) for 3 days, after which time only
22 mg (2.3%) remained.
13.
At this point a turbid solution formed.
14.
Yields are adjusted for 99 wt% starting material and do not account for purity of products.
15.
4-Bromobenzaldehyde has the following properties: mp (DSC) 58-59 °C;
1H NMR
pdf(400 MHz, DMSO-
d6) δ: 7.81-7.86 (m, 4 H), 9.99 (s, 1 H);
13C NMR
pdf(100 MHz, DMSO-
d6) δ: 128.9, 131.4, 132.5, 135.3, 192.5; Anal. Calcd. for C
7H
5BrO: C, 45.44; H, 2.72. Found: C, 45.33; H, 2.82.
16.
The progress of the reaction is followed by TLC analysis on silica gel with 50% EtOAc-hexane as an eluent and visualization with a UV lamp at 254 nm and molybdatophosphoric acid. The alcohol starting material has R
f = 0.45, the aldehyde intermediate has R
f = 0.74 and the acid product has R
f = 0.12. The reaction progress can also be monitored at λ = 260 nm using an Agilent 1100 HPLC equipped with a diode array detector and an Agilent ZORBAX SB-Phenyl column (3.5 μm, 4.6 x 150 mm). Mobile phase: water / acetonitrile (0.1% TFA each). Linear Gradient: Aqueous phase from 30% to 95% over 15 min, then back to 30% over 0.5 min, and holding at 30% for an additional 4.5 min (total method time of 20 min isothermally at 30 °C). COOH λ
max = 245 nm, CHO λ
max = 260 nm. Elution times: ROH - 5.6 min , RCOOH - 6.4 min, RCHO - 8.2 min.
17.
4-Bromobenzoic acid has the following properties: mp 247-250 °C;
1H NMR
pdf(400 MHz, DMSO-
d6) δ: 7.70 (d,
J = 8.6 Hz, 2 H), 7.86 (d,
J = 8.6 Hz, 2 H), 13.16 (s, 1 H);
13C NMR(400 MHz, DMSO-
d6) δ: 127.1, 130.2, 131.5, 131.9, 166.8; Anal. Calcd. For C
7H
5BrO
2: C, 41.82; H, 2.51. Found: C, 41.83; H, 2.58.
Handling and Disposal of Hazardous Chemicals
The procedures in this article are intended for use only by persons with prior training in experimental organic chemistry. All hazardous materials should be handled using the standard procedures for work with chemicals described in references such as "Prudent Practices in the Laboratory" (The National Academies Press, Washington, D.C., 2011 www.nap.edu). All chemical waste should be disposed of in accordance with local regulations. For general guidelines for the management of chemical waste, see Chapter 8 of Prudent Practices.
These procedures must be conducted at one's own risk. Organic Syntheses, Inc., its Editors, and its Board of Directors do not warrant or guarantee the safety of individuals using these procedures and hereby disclaim any liability for any injuries or damages claimed to have resulted from or related in any way to the procedures herein.
3. Discussion
Many excellent methods have been reported for the alcohol oxidation reaction, which is one of the simplest transformations in synthetic organic chemistry.
2 However, there is a strong need for more efficient, chemoselective and greener methods that do not require heavy metallic species for such transformations, particularly in the pharmaceutical industry.
3 Also, selective cascade oxidative transformations of alcohols to carbonyl compounds (i.e.
primary alcohols → aldehydes → carboxylic acids, etc.) would be powerful tools, since the target molecule can be obtained directly in a one-pot sequence. The transition metal- or nitroxyl radical-catalyzed oxidation of alcohols to ketones or aldehydes has attracted great attention because
aqueous H2O2 or gaseous O2 can be used as a stoichiometric oxidant.
2 However, it is technically difficult to control the amount of gaseous O
2 added as an oxidant. Moreover,
aqueous H2O2 and gaseous O2 are often concentrated under evaporation and high pressure to increase their respective reactivities, but such treatments can be dangerous because of their explosiveness due to static electricity, heating, shock, etc. In contrast, Oxone (2KHSO
5•KHSO
4•K
2SO
4) offers several advantages with regard to safety, stability, ease of transport, simple handling, controllable addition, nontoxic nature, etc., although aqueous H
2O
2 and gaseous O
2 are more atom-economical than Oxone.
Recently, we reported a highly efficient and chemoselective oxidation of various alcohols to carbonyl compounds such as aldehydes, carboxylic acids, and ketones with powdered Oxone in the presence of catalytic amounts of 2-iodobenzenesulfonic acid or its sodium salt under nonaqueous conditions.
4 Cycloalkanones can be further oxidized to cycloalkenones and lactones by controlling the amount of Oxone used under the same conditions as above. The oxidation rate in IBS-catalyzed oxidation was further accelerated by the use of
powdered Oxone due to its increased surface area.
2-Iodoxybenzenesulfonic acid (IBS)5 as iodine(V), which is generated in situ from 2-iodobenzenesulfonic acid and Oxone, serves as the actual catalyst for the alcohol oxidation (Scheme 1).
4,6
Scheme 1. Proposed Mechanism of In Situ-Generated IBS-Catalyzed Alcohol Oxidation
Various structurally diverse secondary and primary alcohols could be oxidized with IBS under optimized conditions (Table 1). Aldehydes readily react with water to give hydrates, which are oxidized to carboxylic acids in the presence of Oxone.
7 According to previously reported IBX-catalyzed alcohol oxidations,
8 it is difficult to selectively oxidize primary alcohols to the corresponding aldehydes or carboxylic acids. Fortunately, as shown in Table 1, not only primary α,β-unsaturated alcohols, such as propargylic and benzylic alcohols, but also aliphatic alcohols could be selectively oxidized to
Table 1. IBS-Catalyzed Oxidation of Primary and Secondary Alcoholsa
a Unless otherwise noted, results in reference 4a are shown. After unsaturated primary alcohol was consumed, H2O was added to accelerate the further oxidation of aldehyde to the carboxylic acid with Oxone (entries 6, 8 and 10). b The reaction was carried out using (-)-menthol (40.4 g, 256 mmol) in the presence of potassium 2-iodo-5-methylbenzenesulfonate. The yield was determined by GC analysis and included epimer (ca. 4%). c The experiments were performed at Nissan Chemical Industries, Ltd. d The reaction was carried out using 2-octanol (10.0 g, 76.8 mmol) in the presence of potassium 2-iodo-5-methylbenzenesulfonate. The yield was determined by GC analysis. e The reaction was carried out as described in experimental procedures above using 4-nitrobenzyl alcohol (6.13 g, 40.0 mmol) in the presence of potassium 2-iodo-5-methylbenzenesulfonate. f The reaction was carried out using 4-phenyl-1-butanol (6.01 g, 40.0 mmol) in the presence of potassium 2-iodo-5-methylbenzenesulfonate (5 mol%) and Na2SO4.4a Aliphatic primary alcohols were slowly added to the reaction mixture to prevent ester formation in the oxidation.
the corresponding aldehydes and carboxylic acids in excellent yield by controlling the amount of Oxone added in the presence of the precatalyst sodium 2-iodobenzenesulfonate (
1-4 mol%): 0.6-0.8 equiv and 1.2 equiv of Oxone were used for selective oxidation to aldehydes and carboxylic acids, respectively (entries 5-12). The present protocol could be applied to the chemoselective oxidation of alcohols bearing several functional or protective groups such as
silyloxy, benzyloxy, ketal, alkenyl, alkynyl, halo, pyridinyl, and thiophene groups.
4
Appendix
Chemical Abstracts Nomenclature (Collective Index Number);
(Registry Number)
; (Registry Number)
Oxone: Potassium peroxymonosulfate sulfate; (37222-66-5)
Potassium 2-iodo-5-methylbenzenesulfonate; (1093215-92-9)
4-Bromobenzyl alcoholBenzenemethanol, 4-bromo-873-75-6
4-Bromobenzaldehyde; (1122-91-4)
4-Bromobenzoic acid; (5
86-76-5 )
 |
Kazuaki Ishihara was born in Aichi, Japan, in 1963, and received his PhD from Nagoya University in 1991 under the direction of Professor Hisashi Yamamoto. He had the opportunity to work under the direction of Professor Clayton H. Heathcock at the University of California, Berkeley, as a visiting graduate student for three months in 1988. He was a JSPS Fellow under the Japanese Junior Scientists Program from 1989 to 1991. After completing his postdoctoral studies with Professor E. J. Corey at Harvard University, he returned to Japan and joined Professor H. Yamamoto's group at Nagoya University as an assistant professor in 1992, and became Associate Professor in 1997. In 2002, he was appointed to his current position as a Full Professor at Nagoya University. His research interests include asymmetric catalysis, biomimetic catalysis induced by artificial enzymes, dehydrative condensation catalysis towards green and sustainable chemistry, and acid-base combination chemistry.
|
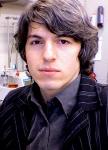 |
Muhammet Uyanik was born in Samsun, Turkey, in 1981 and received his PhD from Nagoya University in 2007 under the direction of Professor Kazuaki Ishihara. He was appointed as an Assistant Professor at Nagoya University in 2007. His research interests includes oxidation reactions and asymmetric catalysis.
|
 |
Richard Crockett was born in North Carolina in 1969 and received his B.S. from University of California, Berkeley in 2002. In the winter of 2003 he began working at Amgen, Inc. as a Process Chemist in the Chemical Process Research and Development group. He is currently a Senior Research Associate for Amgen.
|
Copyright © 1921-, Organic Syntheses, Inc. All Rights Reserved