Org. Synth. 2013, 90, 62-73
DOI: 10.15227/orgsyn.090.0062
Synthesis of N-Acetyl Enamides by Reductive Acetylation of Oximes Mediated with Iron(II) Acetate: N-(1-(4-Bromophenyl)vinyl)acetamide
Submitted by Wenjun Tang
1, Nitinchandra D. Patel, Andew G. Capacci, Xudong Wei, Nathan K. Yee, and Chris H. Senanayake.
Checked by Christopher Haley, Hendrik Klare, and Brian Stoltz.
1. Procedure
A. 1-(4-Bromophenyl)ethanone oxime (1). A 1000-mL single-necked, round-bottomed flask equipped with a 7 cm magnetic stir bar, a 50-mL pressure-equalizing dropping funnel fitted with a nitrogen inlet adapter, and an ice-water bath, is charged with 1-(4-bromophenyl)ethanone (50.0 g, 251 mmol, 1 equiv) (Note 1), hydroxylamine hydrochloride (37.0 g, 532 mmol, 2.1 equiv) (Note 2) and denatured ethanol (375 mL) (Note 3). Pyridine (37.5 mL, 465 mmol, 1.85 equiv) (Note 4) is charged through the pressure-equalizing dropping funnel to the suspension over 5 min. Once the addition is complete, the dropping funnel is replaced by a water-cooled condenser fitted with a nitrogen inlet adapter. The ice-water bath is replaced by an oil bath and the reaction mixture is heated at reflux under nitrogen for 4 h (Note 5). After this period, the flask is removed from the oil bath and is placed in an ice-water bath until the internal temperature cools to approximately 20 °C Temperature of the mixture was determined by addition of a thermometer to the flask after approximately 10 min of cooling. The magnetic stir bar is removed and the reaction mixture is concentrated by rotary evaporation (60 °C, 35-40 mmHg) to remove ethanol and other volatiles (~370 mL) to provide a solid residue. The flask is equipped with 7 cm magnetic stir bar and a 500-mL pressure equalizing dropping funnel. Water (375 mL) is charged to the mixture through the dropping funnel over 15 min. The resulting slurry is stirred at room temperature for 1 h, then vacuum-filtered on a 9-cm Büchner funnel (fitted with Whatman-1 filter paper, 90 mm), washed with water (2 x 25 mL) and suction dried (approx. 10 min). The solid is transferred to a 250-mL beaker and dried under vacuum (~130 mmHg) at 65 °C for 12 h to afford the title compound 1 as a white solid (53.0-53.1 g, 99%) (Note 6).
B. N-(1-(4-Bromophenyl)vinyl)acetamide (2). An oven-dried 1000-mL, three-necked, round-bottomed flask equipped with 7 cm magnetic stir bar, an internal thermometer, a rubber septum and a reflux condenser fitted with a nitrogen inlet, is charged 1-(4-bromophenyl)ethanone oxime (1, 20.0 g, 93.4 mmol, 1 equiv) and THF (125 mL) (Note 7) to give a clear solution. To the stirred solution are added acetic anhydride (19.1 g, 17.6 mL, 187 mmol, 2.0 equiv) (Note 8) and acetic acid (16.8 g, 16.0 mL, 280 mmol, 3.0 equiv) (Note 9). The resulting solution is sparged with nitrogen for 20 min (Note 10) and then iron(II) acetate (32.5 g, 187 mmol, 2.0 equiv) (Note 11) is charged in one portion. The resulting brown slurry is heated to approximately 65 °C with a heating mantle and stirred for 12 h under a nitrogen atmosphere (Note 12). The heating mantle is then replaced with an ice-water bath and the resulting mixture is cooled to an internal temperature of approximately 5 °C. To this solution is charged ethyl acetate (100 mL) (Note 13) and then water (200 mL) slowly over 10 min while keeping the internal temperature below 20 °C (Note 14). The pH of the solution is adjusted to ~5 by the addition of 25 mL of 15 wt% aqueous NaOH solution (Note 15). The contents are transferred to a 1-L separatory funnel and the layers are separated. The bottom aqueous layer is extracted with ethyl acetate (125 mL). The combined organic layers are washed sequentially with 1 N aqueous NaOH solution (120 mL) followed by 8 wt% aqueous sodium bicarbonate solution (150 mL) (Notes 16 and 17). The organic layer is dried over anhydrous sodium sulfate (5 g) (Note 18) and filtered. The filtrate is transferred into a 500-mL round-bottomed flask and concentrated by rotary evaporation (40 °C, 25 mmHg) to dryness (Note 19). To the residue is charged ethyl acetate (10 mL) followed by hexanes (95 mL) using a 250 mL addition funnel over a period of 30 min while stirring with a 7 cm magnetic stir bar. The resulting slurry is stirred for 3-4 h at ambient temperature, and then vacuum-filtered on a 6-cm Buchner funnel (fitted with Whatman-1 filter paper, 60 mm). The cake is rinsed sequentially with 30 mL of hexanes/ethyl acetate (5:1 v/v) (Note 20) and 15 mL of hexanes and is suction dried (ca. 10 min). The solid is transferred into a 50-mL round-bottomed flask and further dried under vacuum (~130 mmHg) at 50 °C for 12 h. The title compound 2 is obtained as an off-white solid (17.25-17.90 g, 77-80%) (Note 21).
2. Notes
1.
1-(4-Bromophenyl)ethanone (98%) was purchased from Sigma Aldrich Co. and used as received.
2.
Hydroxylamine hydrochloride (99%) was purchased from Alfa Aesar and used as received.
3.
Denatured ethanol (contains ~5% methanol and ~5% isopropanol as denaturants) was purchased from Sigma-Aldrich Co. and used as received.
4.
Pyridine (anhydrous, 99.8%) was purchased from Sigma-Aldrich Co. and used as received.
5.
The oil bath was heated at 85 °C. All solids dissolve and give a clear solution when the temperature of the oil bath reached approx. 35 °C. The progress of the reaction was monitored by HPLC, (Hewlett Packard 1100, Halo C
8 4.6 mm x 150 mm, 2.7 µm column) by using a liner gradient of B (H
2O with 0.4 % HClO
4) and A (acetonitrile) at a flow rate of 1.2 mL/min with UV detection at 220 nm and column temperature of 20 °C; liner gradient, 85-2% B, 7 min).
|
Compound |
Retention time (min) |
|
1-(4-Bromophenyl)ethanone |
5.28 |
1-(4-Bromophenyl)ethanone oxime (1) |
6.19 |
N-(1-(4-Bromophenyl)vinyl)acetamide (2) |
4.70 |
|
6.
The product displayed the following physical and spectroscopic properties: mp 120-122 °C; Lit.
2 mp 128-130 °C;
1H NMR
pdf (400 MHz, DMSO-d
6) δ: 2.13 (s, 3 H), 7.55-7.63 (m, 4 H), 11.33 (s, 1 H);
13C NMR
pdf (100 MHz, DMSO-d
6) δ: 11.36, 121.94, 127.57, 131.30, 136.14, 152.09; [M + H]
+ calcd for C
8H
8NOBr: 213.9862. Found: 213.9857. Anal. Calcd. For C
8H
8NOBr C, 44.89, H, 3.77, N, 6.54; found C, 44.97, H, 3.80, N, 6.48.
7.
Anhydrous THF (≥99.9 %) was purchased from Sigma-Aldrich Co. and used as received.
8.
Acetic anhydride (reagent ACS grade, 97+ %) was purchased from ACROS and used as received.
9.
Glacial acetic acid (min 99.7 %) was purchased from EMD Chemicals Inc. and used as received.
10.
It is recommended to sparge the solution with nitrogen thoroughly for approx. 20 min before charging iron(II) acetate into the solution.
11.
Iron(II) acetate (anhydrous, 97 %) was purchased from Strem Chemical Co. and used as received. Iron (II) acetate is air and moisture sensitive; hence, it must be stored under nitrogen or argon and handled with minimum exposure with air.
12.
Keep reaction under nitrogen atmosphere all the times.
13.
Ethyl acetate (ACS reagent grade, ≥ 99.5 %) was purchased from EMD Chemicals Inc. and used as received.
14.
An exotherm is observed during water addition (~10 °C).
15.
Sodium hydroxide (pellets, 99.1 %) was purchased from Fisher Scientific and used as received to prepare 15 wt% and 1 N NaOH aq. solutions.
16.
Sodium bicarbonate (white powder, min 99.7 %) was purchased from EMD Chemicals Inc. and used as received to prepare 8 wt % aqueous solution.
17.
The pH value of the aqueous solution should be ~8 after wash. If the aqueous layer remains acidic, wash again with 8 wt % sodium bicarbonate solution until the pH of the aqueous solution reaches ~8.
Caution: Carbon dioxide is released during the wash.
18.
Anhydrous sodium sulfate powder is purchased from EMD Chemicals Inc. and used as received.
19.
The pale orange oil solidified upon cooling to give a beige solid.
20.
Hexanes (ACS grade) was purchased from Sigma-Aldrich Co. and used as received.
21.
The product displayed the following physical and spectroscopic properties: mp 106-113 °C;
1H NMR
pdf (400 MHz, CDCl
3) δ: 2.06 (s, 3 H), 5.07 (s, 1 H), 5.73 (s, 1 H), 7.11 (s, 1 H), 7.25 (d,
J = 8.3 Hz, 2 H), 7.46 (d,
J = 8.4 Hz, 2 H),
13C NMR
pdf (75 MHz, CDCl
3) δ: 24.48, 103.82, 122.74, 127.78, 131.83, 137.18, 139.75, 169.32. [M + H]
+ calcd for C
10H
10NOBr: 240.0019. Found: 240.0009; Anal. Calcd. For C
10H
10NOBr C, 50.02, H, 4.20, N, 5.83; found C, 49.99, H, 4.19, N, 5.70. Note: It was found that compound
2 was prone to tautomerize in sufficiently acidic CDCl
3.
Handling and Disposal of Hazardous Chemicals
The procedures in this article are intended for use only by persons with prior training in experimental organic chemistry. All hazardous materials should be handled using the standard procedures for work with chemicals described in references such as "Prudent Practices in the Laboratory" (The National Academies Press, Washington, D.C., 2011 www.nap.edu). All chemical waste should be disposed of in accordance with local regulations. For general guidelines for the management of chemical waste, see Chapter 8 of Prudent Practices.
These procedures must be conducted at one's own risk. Organic Syntheses, Inc., its Editors, and its Board of Directors do not warrant or guarantee the safety of individuals using these procedures and hereby disclaim any liability for any injuries or damages claimed to have resulted from or related in any way to the procedures herein.
3. Discussion
Syntheses of
N-acetyl enamides have gained increasing attention due to their importance as the starting materials for making chiral amines by asymmetric hydrogenation. Several preparative methods are available, including: 1) direct condensation of acetamides with ketones;
3 2) addition of an organometallic reagent to a nitrile followed by quench of the resulting imine with an electrophile;
4 3) transition metal-catalyzed coupling of vinyl derivatives such as vinyl halides,
5 triflates,
6 or tosylates
7 with amides; 4) Heck arylation of vinylacetamide;
8 5) reductive acylation of ketoximes.
9 While most of these methods suffer from a limited substrate scope, low yields, high cost, or the requirement of cryogenic conditions, the reductive acylation of ketoximes with Fe/Ac
2O/AcOH proved to be economical and tolerant of various functionalities, and is often the method of choice at a laboratory scale.
9a-d However, this method is not amenable to scale-up. The uncontrollable initiation of iron powder often leads to inconsistent yields and impurities. Singh and coworkers
9f reported a method in which pyrophoric phosphine is used as the alternative reducing reagent. Hydrogen was also reported as the reducing source, primarily for the synthesis of cyclic enamides.
9g A CuI-catalyzed method with NaHSO
3 as the reducing reagent was also reported.
9h
The procedure presented herein employing iron(II) acetate as the reducing reagent offers several advantages over the Fe/Ac
2O/AcOH method.
10 First of all, its mild reaction profile is reliable and amenable to scale-up activities. Additionally, the purification procedure is simpler since both iron(II) acetate as the reagent and iron(III) acetate as the side-product are water-soluble. Higher yields are achieved for most substrates because of the mild reaction conditions (
Table 1 and
Table 2).
Table 1. Synthesis of acyclic N-acetyl α-arylenamidesa
Table 2. Synthesis of acyclic N-acetyl α-arylenamidesa
Appendix
Chemical Abstracts Nomenclature (Collective Index Number);
(Registry Number)
1-(4-Bromophenyl)ethanone: Ethanone, 1-(4-bromophenyl)-; (99-90-1)
Hydroxylamine hydrochloride: (5470-11-1)
1-(4-Bromophenyl)ethanone oxime: Ethanone, 1-(4-bromophenyl)-, oxime; (5798-71-0)
Iron(II) acetate: Acetic acid, iron(2+) salt (2:1); (3094-87-9)
N-(1-(4-Bromophenyl)vinyl)acetamide: Acetamide, N-[1-(4-bromophenyl)ethenyl]-; (177750-12-8)
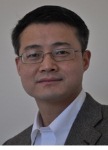 |
Dr. Wenjun Tang was born in 1974 in Zhejiang Province, China. He received his B.Eng. degree in 1995 from East China University of Sciences and Technology and his M.S degree in 1998 in Chemistry from Shanghai Institute of Organic Chemistry, Chinese Academy of Sciences, where he worked with Professor Dawei Ma. He was awarded his Ph.D. in 2003 from The Pennsylvania State University for his work in asymmetric catalysis with Professor Xumu Zhang. After two-year postdoctoral research with Professor K. C. Nicolaou at the Scripps Research Institute, he joined the Department of Chemical Development at Boehringer Ingelheim Pharmaceuticals Inc, where he is currently Principal Scientist. His research interests include development of efficient chemical processes, asymmetric synthesis and catalysis, and chiral ligand design. |
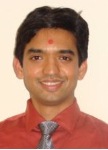 |
Nitinchandra D. Patel was born in 1980 in Ahmedabad, India. He received his B.Eng. degree in 2001 in Chemical Engineering from Nirma Institute of Technology, Ahmedabad, India. He then moved to USA and joined M.S. program at Texas A & M University-Kingsville, where he obtained his M.S. degree under the guidance of Dr. Apurba Bhattacharya in 2005. Since then, he has been a process chemist at Boehringer Ingelheim Pharmaceuticals Inc. in Ridgefield, Connecticut. His research focuses on the design and development of practical synthetic methods to drug candidates. |
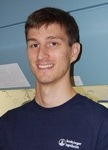 |
Andrew Capacci was born in Maryland in 1987 and moved with his family to Alaska in 1988. He received his bachelor's degree from the University of Toronto in 2009 where he performed undergraduate research with Professor Mark Lautens. He then undertook an internship at Boehringer Ingelheim Pharmaceuticals, Inc. under the supervision of Dr. Wenjun Tang. He is currently a graduate student at Princeton University with Professor David MacMillan. |
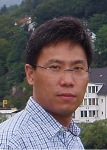 |
Dr. Xudong Wei is currently a Senior Principal Scientist and project leader in Boehringer-Ingelheim Pharmaceuticals working on the large-scale synthesis of active pharmaceutical ingredients. He received his BS and PhD degrees from Nanjing University in China and subsequently worked there as an Associate Professor for two years. He did postdoctoral research at Tübingen University, the University of York and Emory University before he joined Boehringer-Ingelheim Pharmaceuticals in Ridgefield, Connecticut in 2001. He is the co-author of >70 research publications and patents. |
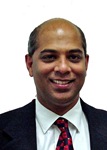 |
Dr. Chris H. Senanayake was born in Sri Lanka. He completed his M.S. at Bowling Green State University, and his Ph.D. under the guidance of Professor James H. Rigby at Wayne State University in 1987. He then undertook a postdoctoral fellow with Professor Carl R. Johnson and worked on the total synthesis of polyol systems such as amphotericin B and compactin analogous, and the synthesis of C-nucleoside precursors. In 1989, he joined the Department of Process Development at Dow Chemical Co. In 1990, he joined the Merck Process Research Group. After six years at Merck, he accepted a position at Sepracor, Inc. in 1996 where he was promoted to Executive Director of Chemical Process Research. In 2002, he joined Boehringer Ingelheim Pharmaceuticals. Currently, he is the Vice President of Chemical Development and leading a group of highly talented scientists, engineers, and administrative staff located in Ridgefield, CT. |
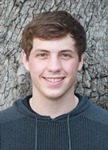 |
Christopher K. Haley was born in Boston, MA in 1987 and received his B.S. degree in chemistry in 2010 from New York University where he conducted research with Professor David I. Schuster. He subsequently joined the laboratory of Professor Brian M. Stoltz at the California Institute of Technology in 2010 where he is currently pursuing his Ph.D. His research interests focus on the methodologies that exploit aryne reactive intermediates in the preparation of benzannulated heterocycles and their application toward the synthesis of biologically active natural products. |
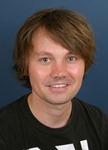 |
Hendrik Klare, born in Ankum, Germany in 1981, studied chemistry at the Westfälische Wilhelms-Universität Münster where he received his diploma in 2007 and his Ph.D. degree in 2011 under the supervision of Professor Martin Oestreich. His graduate research included the exploitation of diverse modes of silane activation for catalysis. As part of its DFG predoctoral fellowship, he also spent six months as a visiting scholar in the group of Professor Kazuyuki Tatsumi at Nagoya University in Japan. After postdoctoral studies with Professor Gerhard Erker at Münster focusing on frustrated Lewis pair chemistry, Hendrik joined the laboratories of Professor Brian M. Stoltz at the California Institute of Technology as a DAAD postdoctoral fellow and is currently involved in the development of novel methodologies for natural product synthesis. |
Copyright © 1921-2025, Organic Syntheses, Inc. All Rights Reserved