Org. Synth. 2013, 90, 96-104
DOI: 10.15227/orgsyn.090.0096
Preparation of 1,5-Disubstituted 1,2,3-Triazoles via Ruthenium-catalyzed Azide Alkyne Cycloaddition
Submitted by James S. Oakdale and Valery V. Fokin
1.
Checked by Satoshi Umezaki and Tohru Fukuyama.
1. Procedure
1-Benzyl-5-phenyl-1H-1,2,3-triazole. Benzyl azide (10.0 g, 75 mmol, 1.0 equiv) (Note 1) is placed in a 500-mL, three-necked round-bottomed flask and equipped with an 8 × 30 mm, octagon-shaped Teflon coated-magnetic stirring bar. The center neck is equipped with a three-way stopcock connected to argon line and bubbler. The other two necks are equipped with a rubber septum. The reaction vessel is purged with argon supplied by an argon filled balloon, after which the three-way stopcock is reconnected. 1,2-Dichlorethane (150 mL) (Note 2) and phenylacetylene (Note 3) (8.06 g, 8.66 mL, 79 mmol, 1.05 equiv) are added sequentially to the flask and the stirred solution is placed in a 45 °C oil bath. After five min, a solution of chloro(1,5-cyclooctadiene)(pentamethylcyclopentadiene)-ruthenium (285 mg, 0.75 mmol, 1 mol %) (Note 4) in DCE (3 mL) is added to the reaction vessel via syringe. The orange solution becomes dark brown (Notes 5 and 6). After 30 min the solution is cooled to room temperature and silica gel (35 g) (Note 7) is added. The solvent is removed by rotary evaporation (35 °C, 40 mmHg). The resulting light brown powder is placed in a 5 cm diameter column and flushed with ethyl acetate (2 × 200 mL). The dark brown solution is concentrated again by rotary evaporation (35 °C, 40 mmHg) to give a dark brown solid. The solid material is transferred to a 250-mL one-necked round-bottomed flask, hexanes (200 mL) are added and the heterogeneous solution is triturated (Note 8) for 15 h. The mixture is filtered using a Büchner funnel, rinsed with hexanes (4 x 25 mL) and dried in vacuo (rt, 18 mmHg) to afford 15.9-16.2 g (90-92%) of the titled compound as a beige powder (Note 9).
2. Notes
1.
The submitters purchased benzyl azide, pract. (94%) from Frinton Laboratories, Inc., and used after flushing the compound through a short column of silica gel with diethyl ether. The submitters noted that three times as much catalyst was needed to complete the reaction without purification. The checkers purchased benzyl azide (97%) from Wako Pure Chemical Industries, Ltd. and used as received.
2.
1,2-Dichloroethane was purchased from Fisher Scientific (certified ACS, submitters) or Kanto Chemical Co., Inc. (>99.5%, conforms to ACS, checkers), and degassed prior to use by bubbling a stream of nitrogen (submitters) or argon (checkers) through the solvent for 1 hour. No precautions were taken to dry the solvent.
3.
Phenylacetylene (98%) was purchased from Acros Organics and used as received.
4.
Chloro(1,5-cyclooctadiene)(pentamethylcyclopentadienyl)ruthe-nium(II) (98%) was purchased from Stream Chemicals Inc. (submitters) or Aldrich Chemical Company, Inc. (checkers) and used as received.
5.
The submitters monitored the reaction by GC-MS. Gas chromatography was performed using a Hewlett Packard 5890A Gas Chromatograph. GC-MS data was recorded on an Agilent 7890A GC system with an Agilent 5975C Inert MSD system operating in the electron impact (EI+) mode. Column; Agilent 19091S-433: 325 °C: 30 m × 320 μm × 0.25 μm, H-5MS 5% phenyl methyl silox. Split Ratio 20:1. Front Inlet; 200 °C. Front Detector FID; 300 °C. Oven program; 50 °C for 2.25 min then 60 °C/min to 300 °C for 4 min. Retention times: phenylacetylene (2.9 min), benzyl azide (4.03 min) and 1-benzyl-5-phenyl-1
H-1,2,3-triazole (6.88 min).
6.
The checkers monitored the reaction by
1H NMR. Chemical shifts of the benzyl proton were used for monitoring: benzyl azide (4.35 ppm) and 1-benzyl-5-phenyl-1
H-1,2,3-triazole (5.55 ppm).
7.
The submitters purchased silica gel 60 from EMD Chemicals Inc.; particle size 40-63 μm. The checkers purchased silica gel (acidic) from Kanto Chemical Co., Inc., particle size 40-100 μm.
8.
Three stir bars (8 × 30 mm, octagon-shaped) were added to the hexane suspension and the mixture was vigorously stirred in order to grind the solid into a fine powder. The submitters note that it is critical that the material be completely solid prior to the addition of hexanes.
9.
1-Benzyl-5-phenyl-1
H-1,2,3-triazole has the following physical and spectroscopic data: mp 76-78 ºC;
1H NMR
pdf (CDCl
3, 400 MHz) δ: 5.55 (s, 2 H), 7.06-7.10 (m, 2 H), 7.24-7.32 (m, 5 H), 7.38-7.47 (m, 3 H), 7.75 (s, 1 H);
13C NMR
pdf (CDCl
3, 100 MHz) δ: 51.7, 126.9, 127.1, 128.1, 128.8, 128.8, 128.9, 129.4, 133.2, 135.6, 138.1; IR (thin film) cm
-1: 1483, 1455, 1435, 1242, 1210, 1126; HRMS (ESI)
m/z calcd. for
C
15H
13N
3Na ([M+Na]
+) 258.1007; found 258.1006; Anal. calcd. for C
15H
13N
3: C, 76.57; H, 5.57; N, 17.86. found: C, 76.57; H, 5.72; N, 17.65.
Handling and Disposal of Hazardous Chemicals
The procedures in this article are intended for use only by persons with prior training in experimental organic chemistry. All hazardous materials should be handled using the standard procedures for work with chemicals described in references such as "Prudent Practices in the Laboratory" (The National Academies Press, Washington, D.C., 2011 www.nap.edu). All chemical waste should be disposed of in accordance with local regulations. For general guidelines for the management of chemical waste, see Chapter 8 of Prudent Practices.
These procedures must be conducted at one's own risk. Organic Syntheses, Inc., its Editors, and its Board of Directors do not warrant or guarantee the safety of individuals using these procedures and hereby disclaim any liability for any injuries or damages claimed to have resulted from or related in any way to the procedures herein.
3. Discussion
Ruthenium-catalyzed azide-alkyne cycloaddition (RuAAC)
2 is a sister process of a widely utilized CuAAC reaction.
3 In contrast to the copper catalysis, which requires the formation of σ-copper(I) acetylides (when terminal alkynes are used), ruthenium catalysts activate alkynes via π-interactions, increasing their nucleophilicity and thereby promoting the addition of the alkyne's most nucleophilic carbon to the electrophilic N3 terminus of the azide. The currently accepted mechanism of the reaction is shown in
Scheme 1.
4 In reactions with terminal alkynes, RuAAC produces 1,5-disubstituted 1,2,3-triazoles (instead of the 1,4-regiosiomers that are the exclusive products of CuAAC). Ruthenium catalysts are also active in the cycloaddition of internal alkynes with organic azides to provide fully substituted 1,2,3-triazoles.
2,4,6 Regioselectivity is often high for unsymmetrically substituted internal alkynes and is generally influenced by the electronic properties of the substituents, their steric demands, and the ability to engage in hydrogen bonding.
2,4-7 Thus, hydrogen bond donors (alcohols and amines) in the propargylic position of the alkyne invariably end up at the C-5 position of the product triazole.
4 This directing effect can be explained by the formation of a strong H-bond between the chloride ligand on the ruthenium and the H-bond donor group. The effect of the electronic properties of the alkyne on regioselectivity is exemplified by reactions of ynones and propiolic esters, which usually result in regioselective formation of substituted triazoles with those groups at the C-4 position of the heterocycle.
Scheme 1. Key intermediates in the RuAAC catalytic cycle.
Among the many ruthenium catalysts that have been examined, only four complexes containing the [Cp*RuCl] fragment proved viable for this reaction: Cp
*RuCl(PPh
3)
2, [Cp
*RuCl]
4,
5 Cp
*RuCl(COD) and Cp
*RuCl(NBD). For a mechanistic study as well as reaction scope and limitations, see references 4,6.
The RuAAC reaction is compatible with a range of aprotic solvents including 1,2-dichloroethane, acetone, toluene, dioxane, dichloromethane, dimethylformamide, and chloroform, and it is important that the solution be completely homogeneous. Water, ethyl acetate, methanol, isopropyl alcohol, hexanes, and diethyl ether were detrimental to the catalysis. The procedures provided in this work call for moderate temperatures of 50 °C; however, for some substrates room temperature is sufficient to achieve high conversions with low catalyst loading. In general, ruthenium complexes containing labile ligands, such as cyclooctadiane, or the "ligand-free" tetramer [Cp*RuCl]4 require lower temperature to achieve full conversion, as opposed to the bis(triphenylphosphine) complexes where it is advisable to perform the reactions at temperatures exceeding 60 °C.
At this stage of development, RuAAC is not as robust as the CuAAC with respect to functional group tolerance and reaction conditions compatibility, primarily due to potential catalyst deactivation, as shown in Scheme 2. For example, organic azides react with 1 to generate ruthenium tetraazadiene complex 2. These complexes are exceedingly stable, can be isolated by column chromatography and are often easily identified by the presence of a green spot on TLC (or a green band on a silica gel column). Thus, the catalyst should not be mixed with the azide in the absence of alkyne.
Scheme 2. Catalyst deactivation pathways in CuAAC.
Ruthenium-catalyzed reactions of alkynes are numerous and have evolved into an extraordinary number of synthetically useful transformations during the last decades. Among them is the cyclotrimerization of alkynes to generate benzene rings (
4),
8 which was shown to proceed through a ruthenacyclopentatriene
3 intermediate.
8c There is no direct evidence that ruthenacycle
3 results in deactivation of the catalyst or is even formed during standard RuAAC reactions. However, an isolated ruthenacycle similar to
3 was catalytically incompetent and also did not react with azides, even at the elevated temperature.
4
Cyclobutadiene ruthenium complex
5 (characterized by X-ray crystallography) was recently isolated from a dimerization reaction of propargylic alcohols.
9 It is a very non-polar compound, stable to column chromatography, and reminiscent of ruthenium species prepared by Kirchner et. al.
10 As with
2 and
3, complex
5 does not react with azides.
Figure 1. Effects of atmospheric oxygen on RuAAC.
Calorimetry trace of the reaction between benzyl azide and phenyl acetylene (0.1M in DCE). Several conditions were examined using 4 mol % catalyst loading (0.004M in DCE) including: degassed DCE under argon, degassed DCE under atmospheric oxygen, untreated DCE under atmospheric oxygen, and untreated DCE under argon. These results illustrate the necessity of placing the RuAAC reaction under an inert atmosphere.
RuAAC reaction is quite sensitive to atmospheric oxygen and must be run under an inert atmosphere. It is known that Cp
*RuCl(PPh
3)
2 reacts with dioxygen to give Cp*RuCl(O
2)(PPh
3), where the dioxygen ligand is reportedly not tightly bound and can be replaced by a phosphite ligand, Cp*RuCl(L)(PPh
3).
11 However, when employing the Cp*RuCl(COD) catalyst the effects of molecular oxygen can be drastic in the RuAAC reaction.
Figure 1 shows the rate profile of the reaction of benzyl azide with phenylacetylene (0.1 M in DCE with 0.004 M Cp
*RuCl(COD), at 45
oC) using reaction heat flow calorimetry. The area under the curve is directly correlated with the overall conversion. As seen in this example, the maximum rate and overall yield is significantly higher when the reaction is performed under argon. The conversion was quantitative under argon and only 20% under air.
The RuAAC process significantly expands the reach of catalytic dipolar cycloaddition reactions. Its applications are beginning to appear
12 and should continue to grow as the reaction matures and new and improved catalysts are developed.
References
Appendix
Chemical Abstracts Nomenclature (Collective Index Number);
(Registry Number)
Benzyl Azide: Azidomethyl benzene;
Triazotoluene; (622-79-7)
Chloro(1,5-cyclooctadiene)(pentamethylcyclopentadienyl)ruthenium(II): (92390-26-6)
Phenylacetylene: Ethynyl benzene;
Acetylene benzen
e; (536-74-3)
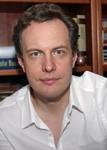 |
Valery V. Fokin received his undergraduate education at the University of Nizhny Novgorod, Russia, and his Ph.D. degree at the University of Southern California under the tutelage of Professor Nicos A. Petasis. After a postdoctoral stint with Professor K. Barry Sharpless at The Scripps Research Institute in La Jolla, California, he joined the Scripps faculty, where he is currently Associate Professor in the Department of Chemistry. His research is focused on new reactivity of organometallic compounds and catalysis, and on applying them to the studies of macromolecular and biological phenomena. His research group is working on the development of new catalytic reactions, asymmetric synthesis, studies of organic and organometallic mechanisms, medicinal chemistry, and smart polymeric materials. |
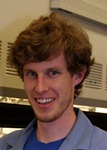 |
James Oakdale received a B.Sc. in chemistry in 2009 from the University of California, Davis, where he pursued undergraduate research in the laboratory of Prof. Mark Kurth. He is currently pursuing a Ph.D. as an NSF graduate research fellow at The Scripps Research Institute under the advisement of Professor Valery V. Fokin. His research efforts include the development and mechanistic investigation of ruthenium catalyzed reactions and the design and manipulation of functional materials. |
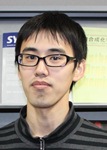 |
Satoshi Umezaki was born in Kumamoto, Japan in 1984. He received his B.S. in 2007 from the University of Tokyo under the direction of Professor Koichi Narasaka. He then moved to the laboratories of Professor Tohru Fukuyama, the University of Tokyo. He received his M.S. in 2009 and he is pursuing a Ph.D. degree. His current research interest is total synthesis of natural products. |
Copyright © 1921-, Organic Syntheses, Inc. All Rights Reserved